How to Design a Mechanical Component in CAD Software (Step-by-Step)
- Bhargava Krishna Marripati
- Feb 16, 2024
- 11 min read
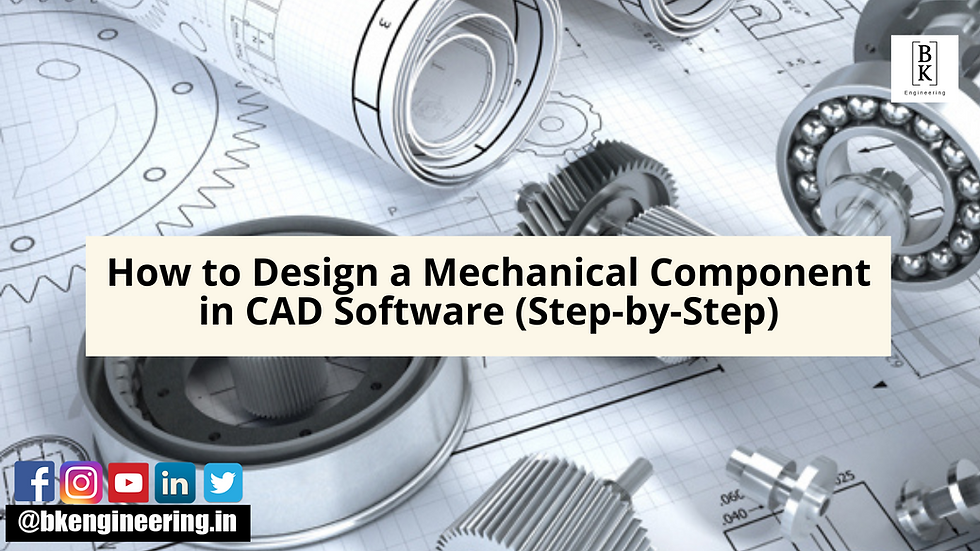
Introduction to CAD Software for Mechanical Design
Computer-aided design (CAD) software is used to create 2D drawings and 3D models of mechanical parts and assemblies. CAD has transformed mechanical design by enabling engineers to draft, analyze, modify, and document their work digitally.
The key benefits of using CAD for mechanical design include:
Increased productivity - CAD allows faster drafting and revisions compared to manual drawing techniques. Complex designs can be created more efficiently.
Improved accuracy - CAD drawings are precise down to the tiniest decimal. Mistakes are minimized compared to hand drafting.
Visualization - CAD allows users to see their 3D models from any angle and visualize how different components fit together. Photo-realistic renderings can also be generated.
Simulation and analysis - CAD models can be tested digitally for interference, stress, fluid flow, motion simulation and other parameters. Virtual testing reduces the need for physical prototypes.
Documentation - CAD integrates modeling with generating drawings, technical illustrations, and Bills of Materials for documentation. All design data is stored digitally.
There are several types of CAD software on the market:
2D CAD focuses on creating flat technical drawings. Mainly used for traditional manufacturing drawings.
3D CAD allows modeling of 3D parts and assemblies. Used for mechanical product design.
Parametric CAD uses parameters and constraints to drive model dimensions. Changes update the entire model.
The major players in CAD software include Autodesk, Dassault Systemes, PTC, Siemens, and Free CAD for open-source options. Choosing the right software depends on specific design needs and budget.
CAD has streamlined mechanical engineering workflows for over 50 years and continues to evolve with new technologies like generative design and virtual reality.
Determine Your CAD Software Requirements
When selecting a CAD software for mechanical design, the first step is determining your requirements based on the intended applications, budget, features needed, and interoperability with other software. Key factors to consider include:
Intended applications - Will you primarily use CAD for 2D drafting or 3D modeling? Is the focus mechanical engineering and product design or architecture and construction? This impacts the feature set needed.
Budget - CAD software ranges from free or low-cost options like Onshape, Fusion 360 and DraftSight to high-end packages like SolidWorks, AutoCAD, and CATIA. Consider long-term costs like annual subscriptions too.
Required features - Consider must-have capabilities like advanced surfacing tools, finite element analysis, kinematic simulation, and generative design. Also assess ease of use and learning curve.
Interoperability - Can the CAD files be exported to universal formats like STEP and IGES for collaboration? Will you need to interface with PDM, PLM, CAM, CAE, and other engineering software?
Platform - Should the CAD software run natively on Mac, Windows or Linux? Is a cloud-based solution preferred for mobility?
Industry-specific tools - Some CAD packages are tailored for specialized fields like automotive, aerospace, architecture, electronics, and industrial machinery.
By balancing all these factors against the type of work you need to do, you can select the right CAD software and avoid paying for unnecessary features. But make sure to choose an adaptable solution as your needs evolve.
Get Set Up with a CAD Workspace
Setting up your CAD workspace properly is crucial for an efficient design process. This involves having the right hardware, installing the software, customizing the interface, and configuring units and settings.
Hardware Requirements
Make sure your computer meets the minimum system requirements for running CAD software smoothly. For most entry-level CAD programs, you'll need:
Processor: Intel Core i5 or AMD Ryzen 5
RAM: 8GB minimum, 16GB recommended
Graphics card: Entry-level GPU like NVIDIA Quadro or AMD Radeon Pro
Storage: 250GB SSD
Display: 1080p monitor 21" or larger
For more advanced CAD software and large assemblies, quad-core processors, 32GB RAM, high-end GPUs, and 4K displays are recommended.
Software Installation and Activation
Once you've purchased the CAD license, download the installer from the vendor's website. Run through the installation wizard, selecting all default options. After installation, you'll be prompted to activate the software via the license key or sign-in. Internet connection is required for activation.
Most CAD apps have a trial option if you want to test before purchasing. Trial periods range from 7 to 30 days.
Customizing the Interface
Tailor the interface to match your workflow preferences. Options like:
Show/hide toolbars
Dock/undock side panes
Customize quick access toolbar
Set dark/light theme
Adjust icon size and style
Save custom interface as a workspace preset.
Units and Document Settings
Configure units as MMGS (millimeters, grams, seconds) or IPS (inches, pounds, seconds) under document properties. Set decimal places and angle format.
For drawings, adjust defaults like:
Page size
Title block style
Text styles
Dimension standards
Save document template with settings.
With the workspace, units and templates configured, you're ready to start designing!
2D Drafting Tools for Mechanical Drawings
Mechanical drawings are essential for communicating design intent and manufacturing requirements. CAD software provides powerful 2D drafting tools to create detailed drawings efficiently. Here are some of the key capabilities you'll want to master:
Sketching
Use sketching tools like lines, circles, arcs, polygons, and splines to create 2D profiles and shapes.
Sketches form the basis for creating 3D models.
Take advantage of automatic constraints like horizontal, vertical, tangent, concentric, parallel etc.
Add precise dimensions to fully define sketches.
Dimensions
Dimension sketches to specify exact lengths, radii, diameters, angles etc.
Use different dimension types like aligned, horizontal, vertical, angular, ordinate etc.
Set dimension text font, style, and location for clarity.
Update dimensions easily if the sketch changes.
Constraints
Apply geometric and dimensional constraints to control relationships between sketch entities.
Use constraints like fix, horizontal, vertical, tangent, concentric, equal, parallel etc.
Constraints help create parametric and editable sketches.
Detail Drawings
Create drawings to show detailed views of the part with critical dimensions.
Project edges or create section views to show hidden features.
Add center marks, hidden lines, surface finishes, and other annotations.
Fabrication Drawings
Generate drawings for welded structures, sheet metal parts, machined components etc.
Include welding symbols, bend lines, surface treatment callouts as needed.
Provide instructions required for manufacturing the part.
With these 2D drafting tools, you can create accurate mechanical drawings that effectively communicate design intent while ensuring manufacturability. Apply dimensions and constraints judiciously to fully define the part geometry. The drawings provide the blueprint for manufacturing components correctly.
3D Mechanical Modeling and Assembly
CAD software provides powerful tools for creating 3D models of mechanical parts and assemblies. Here are some of the key capabilities for 3D mechanical design:
Extruding 2D Sketches
One of the most fundamental 3D modeling techniques is extruding a 2D sketch. This allows you to take a 2D shape like a rectangle, circle or irregular sketch, and pull it out into the third dimension to create a 3D solid. You can define the extrusion distance and direction.
Revolving Sketches
Another way to generate a 3D solid is to revolve a 2D sketch around an axis. This allows you to sweep the sketch 360 degrees to create a symmetrical 3D object like a cylinder, cone or sphere.
Cutting, Fillets and Chamfers
You can use extrude cut, revolve cut and other Boolean operations to cut 3D geometry from your parts. This is useful for hollowing out areas or creating complex non-uniform shapes. Fillets and chamfers allow you to ease sharp edges and corners.
Patterns and Arrays
You can quickly create repetitive features like holes, ribs or other extruded objects by using circular, linear or rectangular patterns. This speeds up the process of generating arrays of identical components.
Imported Parts
Most CAD systems allow you to import standard parts from online catalogs. Inserting nuts, bolts, bearings and other purchased components makes assembly easier.
Mating and Constraining
The assembly environment provides tools for mating (joining) parts together by aligning surfaces, axes, edges, etc. You can define movement constraints like hinges and sliders to simulate motion.
With these CAD tools, you can construct detailed and accurate 3D models of complex mechanical components ready for photorealistic rendering, engineering analysis or manufacturing. Proper modeling techniques take practice but allow for efficient design.
Best Practices for Mechanical CAD Projects
To implement effective modeling and design workflows in CAD for mechanical projects, you should follow some standard practices and conventions used by CAD professionals and engineers. This helps ensure your models meet design intent, remain well-organized, and can be shared and reused easily.
Modeling Workflows
Start with simple 2D sketches and extrude them into 3D features. Build models using a bottom-up approach, starting from basic features and building them up into complex components.
Use geometric and dimensional constraints in sketches. This defines intended behavior and makes sketches more robust.
Model parts in context when possible. Sketch on existing geometry of the part to add features.
Use parent/child relationships between features. Edit parent features to automatically update children.
Employ best modeling techniques like removing redundant geometry, combining overlapping features, and minimizing sketch constraints. This creates efficient, robust models.
Design Intent Organization
Name parts, features, sketches, and assemblies in a logical way. This makes their purpose clear.
Add comments to explain the reason for modeling steps. This captures design intent.
Make output templates with custom views, annotations, and layouts. This ensures consistency in drawings.
Organize parts into assemblies with a logical product structure using sub-assemblies when needed.
Collaboration Standards
Develop modeling and drawing standards upfront for conventions, dimensions, tolerances, annotations, etc.
Break large projects into modules for designers to work on separately before bringing together.
Use external references in place of inserting parts into an assembly. This reduces file size and aids sharing.
Create a Central model as a single source of truth that team members contribute updates to often.
Following these best practices will ensure your CAD models meet requirements, can be understood by others, and enable seamless collaboration on mechanical projects.
Advanced CAD Techniques and Tools
CAD software offers advanced modeling capabilities beyond basic part design. Mastering these tools will make you a more efficient CAD designer.
Surfacing
Surface modeling creates smooth, organic 3D shapes. You sketch curves to define edges then create complex surfaces between them. This technique is great for industrial design, consumer products, car bodies, aircraft fuselages, and other freeform shapes. Popular surface tools in CAD include:
Boundary surface - Creates a surfaceconstrained by boundary edges
Lofted surface - Generates a surface between multiple cross section curves
Swept surface - Sweeps a curve along a path to create a surface
Filled surface - Fills an area bounded by 3D curves
Sheet Metal Design
Sheet metal tools allow you to model sheet metal parts with custom bends, punched holes, and formed edges. You can flatten the 3D model to generate 2D fabrication drawings automatically. Sheet metal design is crucial for enclosures, brackets, chassis, HVAC ducts, and more.
Mold Design
Some CAD packages integrate mold design tools for modeling mold halves, cores, cavities, cooling channels, ejector pins, and other mold components. You can analyze draft angles, surface finish, and other manufacturability requirements. Mold tools streamline the process of designing plastic injection molds, die casts, and more.
Casting Design
Casting design tools are used to model cast parts and simulate the casting process. You can add draft angles, fillets, radiuses, and other features to optimize the part for manufacturability as a metal casting. Some CAD software generates gating, runner, and sprue systems for the mold.
FEA Simulation
CAD integrates with Finite Element Analysis (FEA) to simulate stress, deflection, vibration, heat transfer and other behaviors of your 3D model under real-world conditions. This allows engineers to optimize the design digitally before making physical prototypes.
PDM Integration
Many CAD programs integrate with Product Data Management (PDM) software to control file versions, workflows, change orders, BOMs, and other documentation for the design team. This improves collaboration and ensures all users are working with the latest correct data.
Plug-Ins and Customization
An active ecosystem of third-party plug-ins extends CAD functionality for specialized applications like CAM, electrical, plant design, and more. APIs allow users to customize the interface, automate repetitive tasks, and streamline workflows through macros and add-ons.
By mastering these advanced tools, you can take your CAD skills to the next level and expand the possibilities for your designs. With dedication and practice, you'll be able to tackle complex geometry and workflows to save time and cost while delivering higher quality.
Generating Drawings and Documentation
Once your 3D CAD model is complete, you'll need to generate 2D drawings and documentation for manufacturing or review. This involves setting up drawing sheets, inserting different orthographic and section views of the model, adding dimensions and annotations, creating a bill of materials (BOM), and exporting the drawings as PDF files.
Setting Up the Drawing Sheet
Start by creating a new drawing file linked to your CAD model. Set up the sheet size, title block details, and projection view. Insert the base 3D model view and arrange additional projected views as needed around it.
Inserting Views
Orthographic views - Top, front, side, isometric
Section views - Cutaway views revealing interior
Detail views - Zoomed in views of specific areas
Auxiliary views - Alternate angle projections
Arrange, align and scale the drawing views for clarity.
Annotations and Dimensions
Add dimensions, centerlines, notes, and labels to identify key features and call out specifications in the drawing.
Bill of Materials
Generate a BOM table outlining all the parts and quantities needed. The BOM can pull attributes like part numbers from the model.
Export as PDF
Once the drawing sheet is fully annotated, export a PDF file for sharing and documentation purposes. The PDF will preserve the vector formatting for printing and production.
Layouts and Templates
Set up templates with title blocks, border, logos etc to reuse for consistency. Create multiple layout tabs to generate several drawing views from a single model.
Generating professional 2D drawings, a BOM, and PDF documentation is critical for manufacturing and collaboration. Take the time to ensure your CAD drawings are clear, complete and follow industry standards.
Preparing CAD Models for Manufacturing
Before sending CAD models to a manufacturer, it is important to do some final checks and preparation to ensure the files are production-ready. Here are some key steps:
Analyze Model Integrity
Conduct thorough interference and collision checks to make sure parts fit together properly and the model has no impossible geometries. Look for gaps, overlaps, inverted faces, self-intersecting features, and other problems that could prevent manufacturing. Run stress, strain, thermal, and other simulations to verify the design withstands real-world forces and environments.
Use Optimal File Formats
Export files to standard, non-proprietary formats compatible with a wide range of CAM, CNC, and other manufacturing software. Common options include STEP, IGES, DXF, or DWG for drawings. For assemblies, consider exporting as a STEP file. Optimize and reduce file sizes where possible.
Coordinate with Manufacturers
Discuss the project with manufacturers early on. Learn about their design rules, tolerances, materials, finishing needs, and other requirements. Incorporate any necessary design changes before finalizing models. Send information on critical dimensions, annotations, surface finishes, and other notes to streamline production.
Add Manufacturing Metadata
Include basic metadata like units, coordinate system, material, color, and configuration. For drawings, make sure to follow drafting standards and fully dimension critical features. Add GD&T (Geometric Dimensioning and Tolerancing) symbols as needed. Insert notes, tables, and other documentation required for manufacturing directly into the CAD files.
Taking the time to validate and prepare CAD files helps avoid costly surprises or production errors down the line. Proactively managing the transition from digital design to physical product improves the manufacturing process and end product quality.
Resources for Improving CAD Skills
There are many resources available to help you improve your CAD skills and grow as a mechanical designer. Here are some of the top resources to consider:
Books
Books are a great way to build foundational CAD knowledge and skills. Some top books for learning CAD include:
CAD For Dummies - Covers the basics of CAD software and modeling in an easy to understand format. Good for CAD beginners.
Mastering Autodesk Inventor - In-depth guide for learning Autodesk Inventor, one of the top CAD packages.
Parametric Modeling with Autodesk Inventor - Focuses on teaching parametric modeling techniques.
Courses
Online courses allow you to learn CAD at your own pace. Look for courses that provide tutorials, exercises, and instructor support. Some options include:
LinkedIn Learning - Wide range of high-quality CAD courses for all levels. Covers multiple CAD packages.
Udemy - Affordable on-demand courses for learning CAD. Often run sales on course packages.
edX - Free CAD courses from top universities like MIT and Purdue. Can upgrade to paid certificate.
Forums
Forums allow you to get answers to specific CAD questions and connect with other users. The Autodesk forums are especially active:
Autodesk Inventor Forum - Active community for Inventor users.
AutoCAD Forums - Help with 2D drafting and other AutoCAD topics.
Fusion 360 Forums - Great resource for Fusion users.
Conferences
Attending a CAD conference lets you learn from industry experts. Top conferences include:
Autodesk University - Major conference hosted by Autodesk for users of its software.
SOLIDWORKS World - Annual event by Dassault Systems for the SOLIDWORKS community.
Siemens PLM Connection - Conferences focused on Siemens PLM software like NX.
Certifications
Getting certified in a CAD package can help validate your skills. Some options include:
Certified SolidWorks Associate - Entry-level SOLIDWORKS certification.
Autodesk Certified User - Certifies skills in AutoCAD, Inventor, Revit and more.
Siemens Certified NX Associate - Validates NX CAD proficiency.
The right mix of books, courses, forums, events, and certifications can take your CAD expertise to the next level. Focus on resources that align with the software and techniques you use most in your work.
Comentários